Products List
What is ventilated corundum brick in the classification of refractory bricks?
Author:sunrise Time:2018-07-03 11:39
For refractory bricks, some conditions of use are due to the high porosity and high gas permeability of the article. At present, steel mills widely use argon-ventilated corundum bricks at the bottom of the ladle, and use gas to blow metal, that is, corundum bricks for gas blowing liquid. With the same particle size, the filler and the binder are used to tightly bond the particles during the sintering process, so that the product becomes a solid block, and the same size of the pellets determines the shape and size of the pores. If it is necessary to increase the air permeability of the product, it is also necessary to add the filler of the burnt-in additive to have the same particle size as the filler, and the shape is the same as the shape.
Porous permeable corundum bricks used to blow metal have certain advantages with corundum-like magnesium. Breathable corundum bricks for industrial applications can be made of 63% fused corundum 80% pellets, industrial alumina (65%) and refractory clay (35%) as a binder, 20%, the binder should be in the barrel mill In the fine grinding together, the content of more than 60μm should not exceed 1%~1.5%. The mud is mixed on a wet mill, requiring 10 minutes of mixing, the moisture content of the mud is 4.3% to 5%, and then sieved on a sieve having a mesh size of 5 mm. The brick is formed on a hydraulic machine with a pressure of 35 MPa, and the density of the brick is 2.60 g/cm3. The product is fired in a tunnel kiln or a downdraft kiln. The firing temperature is 1570 ° C, the temperature is kept for 22 ± 2 h, and the total firing time is not less than 150 h.
There are many ways to manufacture ventilated corundum bricks. The 20% binder is prepared by co-milling corundum waste (60%) and clay (40%). The moisture content of the mud is 4%~5%, and the density of the pressed bricks is It is 2.60 g/cm3: it is fired in the tunnel kiln for 86h, the highest firing temperature is 1560 °C, and the temperature is kept (5±1)h.
Others use fused corundum as aggregate, pure calcium aluminate cement and SiO2 ultrafine powder as binder, phosphate as dispersant, and ultra-low cement castable process.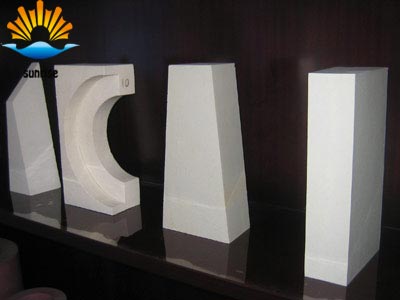
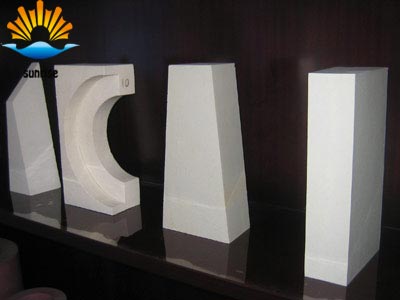